|
Nanjing Anyun electromechanical Co. Ltd. @ Copyright 2014 ICP 08113552; Su |
Address: Nanjing Gulou District No. 70 Qingjiang road Hehai technology R & D Building 8 floor |
Fax: 025 - 83752998 Email: sales@anyunchina.com Website: http://www.anyunchina.com Design by: sunshine network |
|
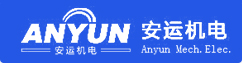 |